Where in the value chain do we find LNG ships?
Shipping LNG overseas is by far the most common way to transport natural gas in liquid form. When LNG plants and fields are situated in remote areas, transportation of LNG by ship is often the preferred, or perhaps even the only, alternative for transporting natural gas. Therefore, LNG ships makes a key link in the LNG value chain, enabling transportation of gas between the liquefaction plant and regasification site.
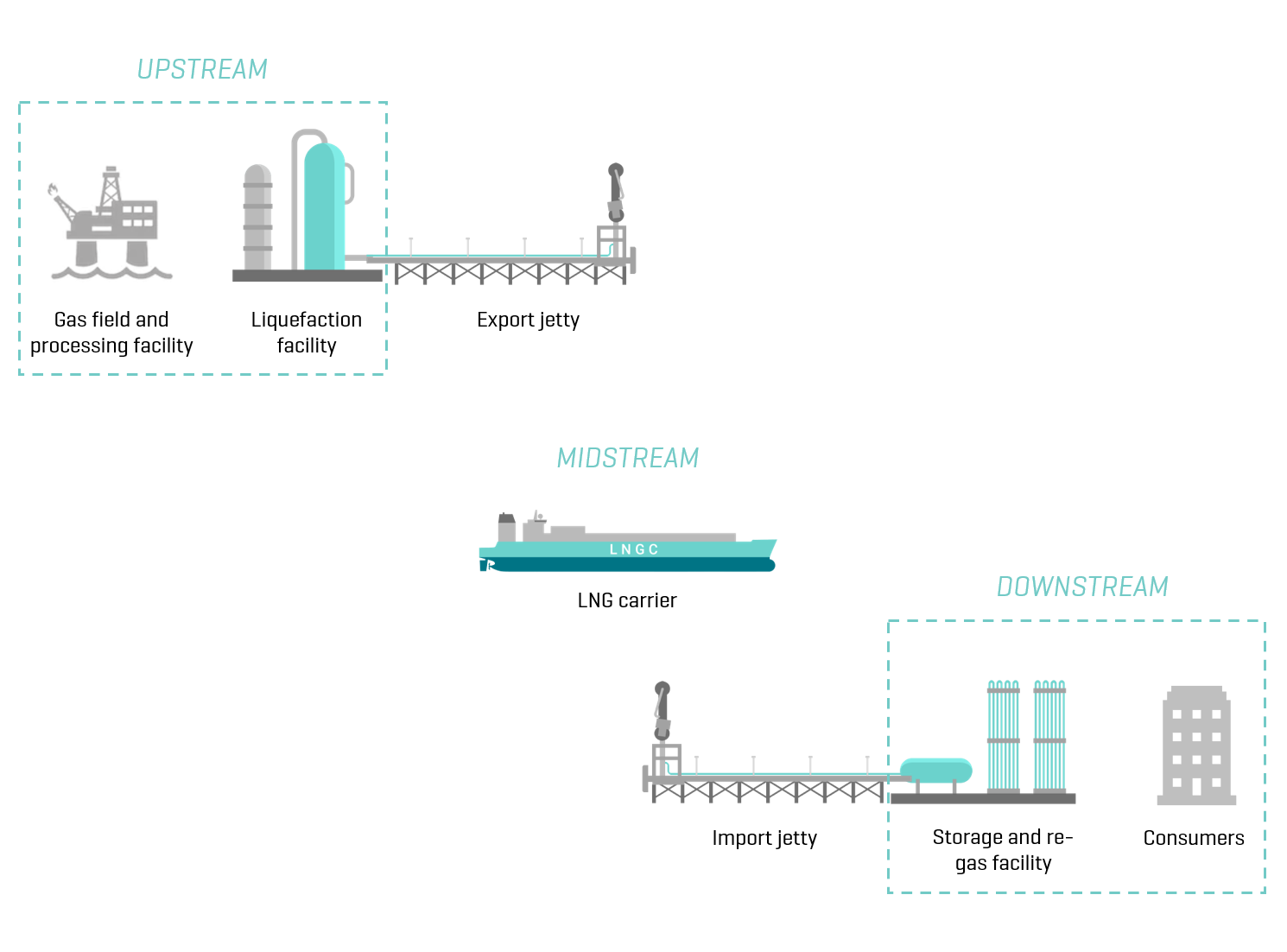
What is an LNG ship?
An LNG ship (or tanker, carrier, vessel) is a ship equipped with containment systems for carrying LNG in bulk. A distinctive feature which separates an LNG ship from other bulk cargo carriers are the heavy insulated, temperature-controlled tanks ensuring the gas is kept in a liquid state at approximately -162 C. The propulsion system of LNG ships is often powered by steam turbines driven by boil-off-gas (BOG) from LNG, boiled liquid fuels such as oil, or a combination. By end 2019, the global LNG fleet consisted of 541 active ships, of which 34 were floating storage regasification units (FSRUs) and 4 were floating storage units (FSUs). The top importing markets of 2019 were Asia Pacific and Asia, while Qatar, Australia and the United States, in that order, were top exporters (IGU, 2020 World LNG Report).
Historically, LNG ships have been operating since the late 1950s, but production first picked up during the 1970s. Since the early 2000s the number of LNG ships delivered per year has drastically accelerated, and so have LNG production scales and vessel sizes. As the LNG industry has been characterized by big scale trades to an increasing extent in recent years, ships with large storage capacities have been a requirement. However, the global LNG fleet ranges from small scale, handysize bulk carriers to large scale carriers, where the world's largest is currently the Mozah, a Q-max ship from Qatargas.
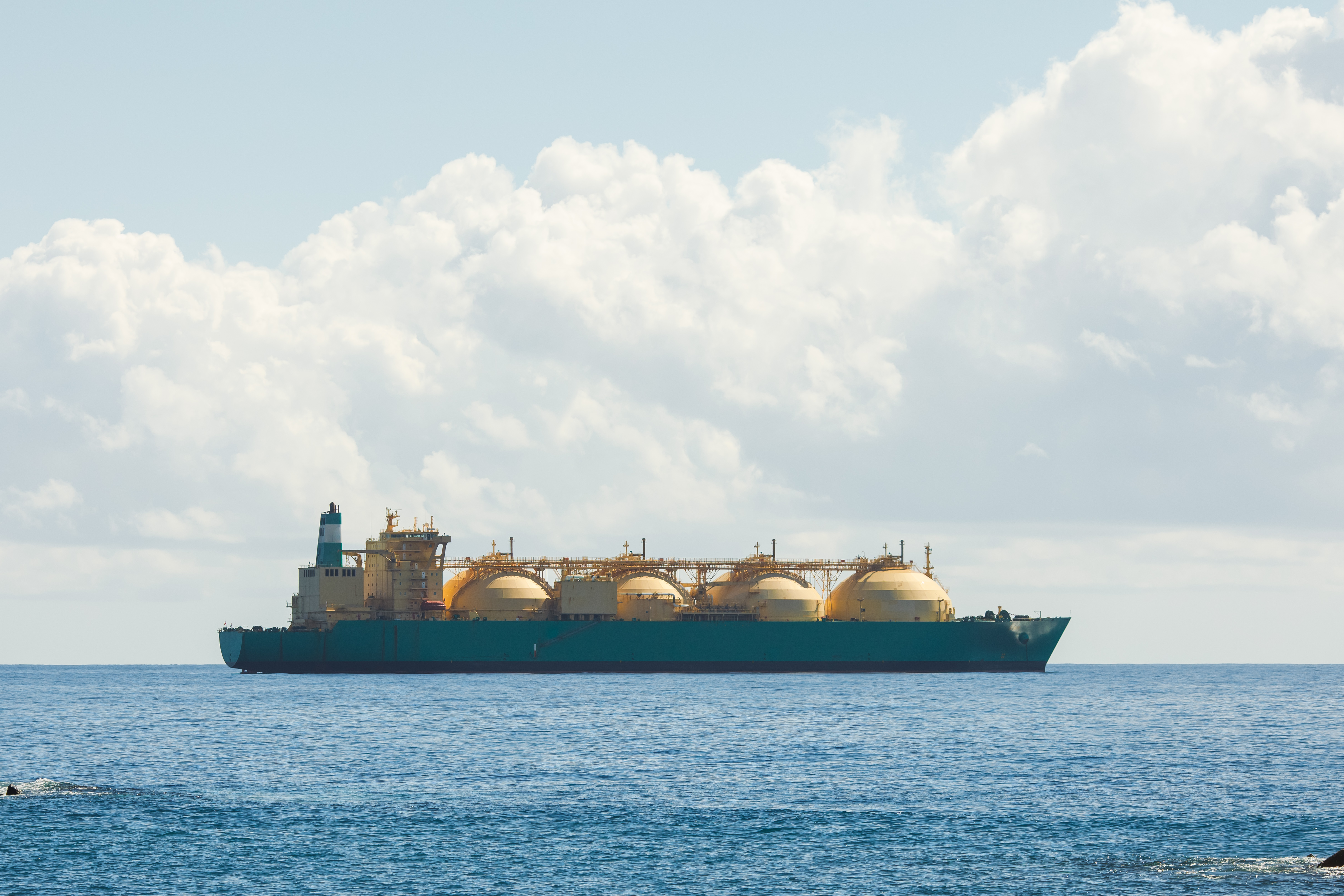
LNG ships are divided into several different types based on their type of cargo tanks
LNG ships are commonly classified based on their tanks, according to International Maritime Organization (IMO) classification of LNG Vessels. The IMO classification generally separates between
- Independent tanks, where the tank is not a part of the ship hull, i.e. they are not crucial to hull strength, and
- Integral tanks, which form a structural part of the ship's hull.
These main classifications of LNG ship tanks can again be further subdivided into different types.
Independent tanks are divided into three types:
- Type A, with design based on classical ship structural design, having quite similar tank arrangement as an oil carrier, with tank design pressure less than 700 mbar. IGC code requires that type A tanks need a full secondary barrier to hold leaks for a minimum of 15 days.
- Type B, either the characteristic spherical Moss-tanks or prismatic IHI SPB tanks. Both require a partial secondary barrier, as opposed to type A, but both operate in pressure below 700 mbar, like type A.
- Type C, based on pressure vessel code and designed to operate above 2000 mbar without any secondary barrier. These tanks can shape as either cylindrical, bilobe or spherical, and due to the lacking secondary barrier, leakage is detected by change in gas composition in hold space, which is equipped with detecting sensors.
Membrane tanks are a type of integral tanks, and there are two common types:
- TGZ Mark III (also referred to as GTT Mark III), designed by Technigaz. The layers of this tank type consist of a primary barrier in stainless steel, primary insulation, secondary barrier within a triplex membrane, secondary insulation and finally the hull structure.
- GT 96 (Also referred to as GTT 96), from Gaztransport. This tank model consists of a primary and secondary membrane by an invariable (in its lack of thermal expansion and contraction) nickel-iron alloy called Invar. The insulation of this model is based on plywood boxes with perlite, flushed with nitrogen gas.
How does the cargo cycle for LNG work?
Due to extremely low operating temperatures, LNG cannot be loaded directly into the ship’s storage tanks without adequate preparations. If not done properly, LNG loading can lead to great thermal stress to tanks and pipes.
To ensure safe loading, a sequence of actions must be followed.
- First, the cargo tanks and hold spaces must be completely cleaned and dried. Impurities and humidity in the tanks from dry docking could cause corrosion, condensation and formation of ice.
- Secondly, inerting of the cargo tanks, insulation spaces and inter barrier spaces is initiated. This basically means inserting a low reactive gas, normally nitrogen gas, which for the cargo tanks is done to reduce moisture and oxygen levels. For the other spaces it prevents corrosion, enables detection of LNG leaks if air composition changes, and prevents formation of a flammable air mix.
- Thirdly, the tanks are “gassed up” by piston purging warm LNG vapor, hence removing remaining inert gas and finish the drying process. The tanks are now ready to be cooled down slowly to about -110C to -130C with LNG vapor.
- Finally, the tanks are ready to be loaded with LNG. The LNG carrier can be loaded by utilizing either a traditional jetty or an innovate jettyless transfer system.
When an LNG ship discharge cargo to an LNG terminal, cargo pumps empty the tanks either completely, or leave a small part of the cargo on board, as a “heel” to be used for tank cooling later.