What does the LNG process look like?
The process described in the following is a generalization of the different links in a typical LNG value chain, deviations from this specifically described process occur.
The LNG process (value chain) can be divided into four main steps;
1. natural gas production and exploration
2. liquefaction and storage
3. shipping
4. receiving, regasification and distribution.
Production and exploration
Production and exploration include extracting raw, unprocessed natural gas from reservoirs, rough on-site processing, and bringing the gas from the site of extraction to a treatment facility, often nearby.
The LNG liquefication process
When brought to the treatment facility or liquefaction plant, hereafter referred to as an LNG plant, the gas is processed and treated through the gas liquefaction cycle, before getting stored and prepared for transport.
Shipping by LNG carriers
Due to capacity and LNG technology like refrigerants and coolers, LNG is most commonly transported using designated LNG carriers, transferring large quantities of LNG by sea. LNG loading takes place at the exporting site and is then shipped to an onshore receiving terminal or an offshore unit with receiving capabilities.
Regasification and distribution
It is then heated for purposes of regasification and prepared for distribution to a gas network, where it can be utilized as fuel for instance for power generation.
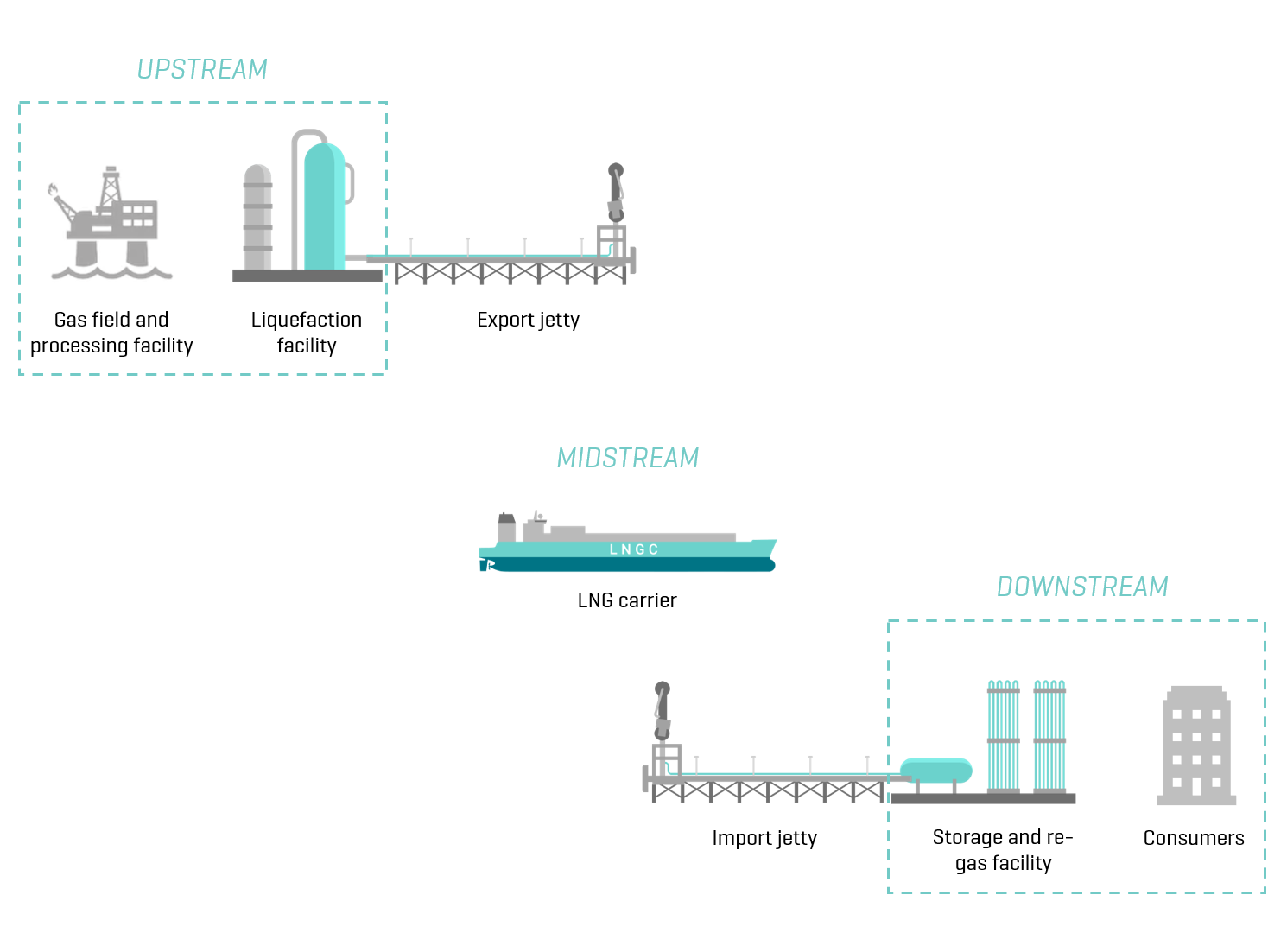
This article will focus on the second link in the chain, namely the process taking place at the LNG plant before shipment.
What is an LNG plant?
The LNG plant makes out the “black box” of LNG production. Completely or partially untreated, raw natural gas in a gaseous state comes in, and refined LNG is shipped out.
In general, two main processes take place at the plant:
1. the gas treatment process
2. the liquefaction process*.
*If natural gas is sold in gaseous state, liquefaction facilities are not necessary. This typically applies to areas with access to a pipeline network.
However, when gas markets and gas fields are far apart, production costs are sufficiently low, and marine ports where a plant can be built is relatively close to the gas field, conditions facilitate LNG production.
Key features in a LNG processing plant
LNG plant sites can be potentially massive in size and make out an expensive part of an LNG project. Production capacity and plant size vary, but key infrastructure in addition to the specific gas treatment and liquefaction equipment include equipment for handling boil-off gas (BOG) like:
- venting
- flaring or re-liquefaction
- send-out-systems
- cryogenic storage tanks.
The individual systems are often closely integrated. The plant also requires infrastructure for LNG loading to ships, which in case either a jetty or the jettyless transfer system can be used.
LNG plants are most commonly placed onshore, but for offshore gas fields, production, treatment, liquefaction, storage and transportation can take place using floating liquefied natural gas (FLNG) facilities.
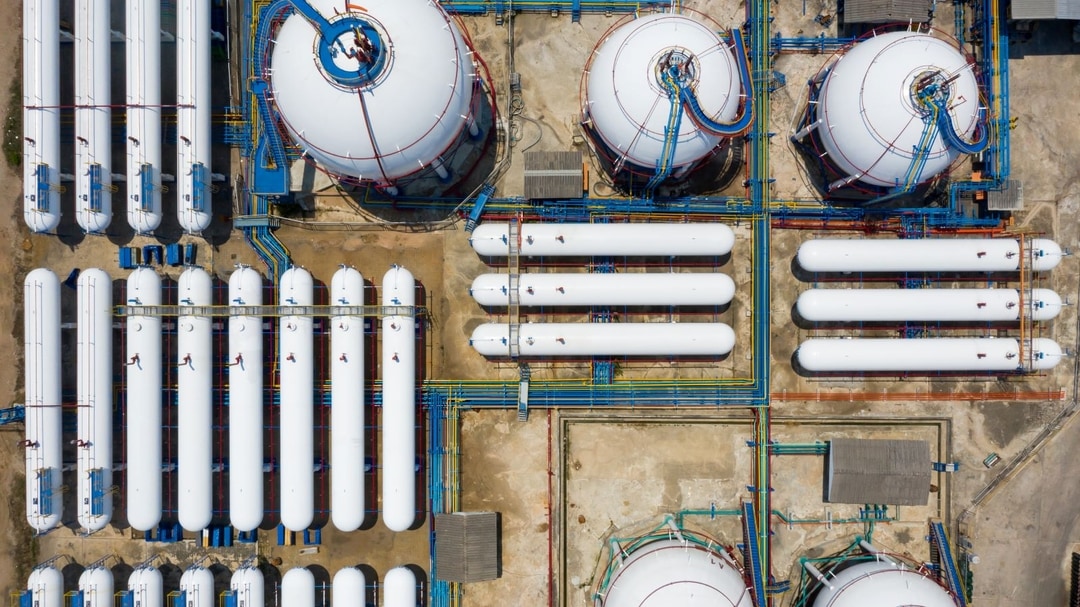
How is LNG extracted and produced?
The well stream of plant feed comes in gaseous form by pipe. Natural gas extracted from the ground contains impurities, water and other associated fluids. This is in general mostly CO2, H2S and Hg. Therefore, before liquefaction can take place, the gas needs to go through a treatment process to remove undesired substances.
The gas goes through a series of vessels, compressors and pipes where gas is stepwise separated from heavier fluids and impurities.
First, water and condensate are removed, followed by removal of acid gas (carbon dioxide, CO2), hydrogen sulfide (HS2) and mercury (Hg). These substances are unwanted, as they may cause ice forming during liquefaction and corrosion in pipelines and LNG heat exchangers.
The remaining mix is precooled, and other, heavier, natural gas liquids are then separated from the mix before liquefaction takes place. Removed hydrocarbons can be stored and sold separately.
The remaining gas mostly consists of methane and some ethane, which is brought to liquefaction.
How does liquefaction of LNG work?
Transporting compressed gas long distances by pipe can be costly and time consuming, but by cooling natural gas to -162°C, it turns into liquid matter, and its volume decreases by 600 times. This makes it possible to transport the gas by ship, and this process is made possible at the LNG plant. The liquefaction and LNG cooling process are based on thermodynamic refrigeration cycles, and takes place in cryogenic heat exchangers, which absorbs heat from the natural gas. Flash gas and BOG can be used as fuel for turbines used for onsite power generation.
We mainly separate between two main types of liquefaction processes:
1. the classical cascade process where different refrigerants which vaporize at different temperatures are used
2. the mixed refrigerant cycle where a continuous, single blend of refrigerants is cooled.
Either way, the end product is LNG, which is stored in cryogenic tanks on site before being shipped off – and converted at an regasification terminal.